It’s all hands on deck down at Rivergate’s shipyard, as contractors are hard at work on MY Kokomo II’s transformation.
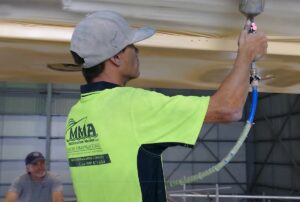
Four months into Kokomo’s refit at Rivergate, we caught up with project manager Marty Johnson to track how the vessel’s overhaul is progressing.
Almost four months into the refit, significant progress has been made – with grafting and fabrication of the new swim platform extension now complete.
Filling, faring and priming of the vessel is also underway to prepare her for an extensive paint job.
While the transom extension is one of the main focuses of this refit, Project Manager Marty Johnson is proud of the critical behind-the-scenes work that’s taking place to both modernise and improve the vessel.
“There’s always challenges with older boats, particularly when it comes to the structural engineering side of things,” says Marty.
“Technology has come a long way since the build of the vessel, and back in the 1980s when the boat was built, some of the structural mechanisms that were implemented are no longer used as best practice… so some of the variation work the team has completed is to ensure the boat meets best practice, especially on items such as the fire hydrants and scupper drains.
“These variations have also made way for some exciting upgrades too, like the lazarette area. It’s now got a washing machine, dryer and a double door fridge freezer – they never had a double door fridge freezer because they never had any room – and now that we’re doing some changes and moving things like dive compressors and hydraulic power packs, we’ve now made room for that.”
When it comes to project management, client satisfaction is top of mind for Marty – and his ultimate goal is to exceed the expectations of owners, captains and crew. Through his weekly meetings with MY Kokomo II’s key stakeholders, it’s clear that Rivergate has ticked all the boxes throughout the refit process.
“Every vessel is different, every crew is different, every captain is different and every owner is different, which of course means every desired outcome is different,” says Marty. “To achieve or exceed an outcome of an owner or vessel’s captain is critical to me. If I can see that within our weekly meetings that the Captain or owner of the vessel is excitable, then I know we’re on the right track. From day one, I’ve seen that excitement from the owners, captain and crew, who have been happy with the vessel’s progress and program.”
As of early September, new electronics have been installed on the vessel, the teak decks have started, a lot of the upstairs faring and painting has been done and the mast is at completion and ready to be refitted once all scaffolding comes down.
If you’re thinking about choosing Rivergate as your superyacht refit destination, rest assured you’re in good hands. Rated as one of the top three shipyards in the world for refit and maintenance, it’s not just the expertise and meticulousness of the tradespeople that ranks highly with owners – it’s also the level of customer service that’s second-to-none.
“Customer service is where Rivergate excels, we go that extra mile for our visiting crew, Captain, owners and the vessels,” says Marty. “We look outside the box. If I see that something could be done better, I’ll make mention of it and raise it with the relevant stakeholders of the ship.”
To learn more about Rivergate’s refit and maintenance services, visit https://rivergate.com.au/shipyard-index#shipyard-overview.
Rivergate will be documenting the transformation of Kokomo II with timelapse cameras, web stories and videos with the tradespeople working on this project, as well as an exclusive interview with Captain Luke Caldwell – coming soon!
Make sure you’re following the Rivergate Facebook, LinkedIn and Instagram accounts to stay up to date on the latest Kokomo II news.